お客様の日常に関わりたい──研究者が語る、フルラベルレスボトル誕生までの軌跡
アサヒ飲料は「アサヒ ラベルレスボトル」の開発、販売をしています。学生時代から環境問題に関心を抱いてきた山口 威仁は、そのプロジェクトに参画するメンバーのひとりです。お客様からの要望が少ない包装部分。だからこそ、その声を大切したい。本プロジェクトの過程を振り返りながら、山口がその想いの丈を語ります。【talentbookで読む】
ラベルレスボトル──それはお客様の潜在的な課題に先手を打った取り組み
アサヒ飲料では、「人にやさしく、地球にやさしい」をコンセプトに、2018年から「ラベルレスボトル」商品を手掛けています。
その中でも、私は「『アサヒ おいしい水』 天然水ラベルレスボトル」において、フルラベルレス化に取り組みました。
そもそもラベルは、リサイクルマークなど必要事項を商品に記載する役割を担っています。また、タックシールやキャップにそれらの情報を記載している場合もあります。しかし、このフルラベルレス商品では、タックシールすらなくしているのです。
一見すると、シールやラベルがなくなっただけですが、これが環境負荷の減少につながっています。さらに、自社の製造面にも良い効果をもたらしています。製造側ではふたつのメリットが生まれました。
ひとつは、ラベルを貼らなくなったため、機械の管理が不要になったことです。もうひとつは、貼り付け漏れがなくなったことです。ラベルは1枚ないだけでも、関係者全員が血眼になって探すほどのことですので、ラベルを無くすことで、他の部分により気を使えるようになり、生産性向上につながりました。
こういった容器・包装の環境配慮やユニバーサルデザインの取り組みは、主に技術研究所やマーケティング部門が中心となり、お客様やバイヤー様の声をもとに開発を進めています。
たとえば技術研究所では、カートン商品の段ボールが開けやすくなるよう、仕様設計などにも尽力しています。とはいえ、段ボールをつくっているメーカーさんは他の飲料メーカーと共通。なので、突出したデザインがつくりにくい側面もありますが、アサヒ飲料独自に改良を進められるように努力を重ねています。
飲料自体の味などと比べ、包装部分はお客様からの声があがりにくい部分です。だからこそ、潜在的な課題に対してどう先手を打って取り組んでいくか考えることになります。それが難しいところですね。
環境に優しいことに取り組みたい──環境を起点に結びつく過去と現在
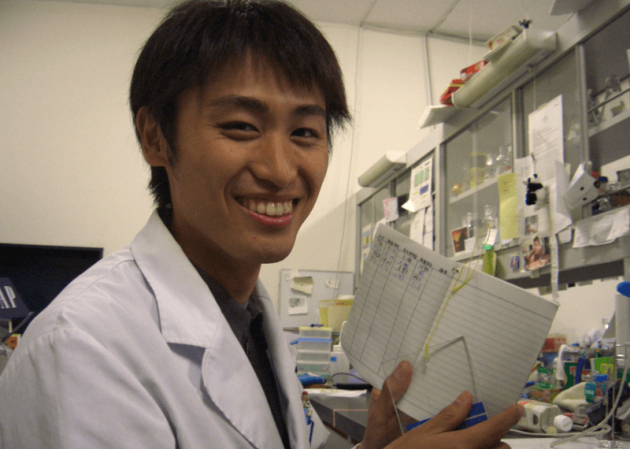
▲学生時代、大学の研究室にて
アサヒ飲料には、2007年に入社しました。
アサヒ飲料に進むきっかけは、大学院での経験にありました。当時は環境を改善する微生物の研究をしていたのですが、研究を進めるうちに、実用化されるまでに50年や100年というスパンがかかることに、やるせなさを感じるようになりました。自分が生きている間に、関わった研究の効果を実感できないと、私自身はモチベーションをあげていくのが難しいと思うようになったのです。
そこで、メーカーに大きな魅力を感じました。消費者の日常に関わることができ、自分の仕事への反応がお客様からすぐ返ってくるからです。
なので、就職活動では飲料会社を一通り見た上で、その他にもビールやお菓子、トイレタリーなどメーカーの商品開発を中心に見ていました。
さまざまな企業を見る中で、コンビニや自販機など日常生活で目に触れる機会が多いのは、飲料会社の商品だと思っていました。そして、知り合いに聞いたり実際に働く人と面接したりして、自分が一番合っていると感じたことが、アサヒ飲料入社の決め手になりましたね。
アサヒ飲料には事務系と技術系のふたつの採用方法があります。私はこれまで研究をしていたので、技術部門の方が経験を生かしやすいと思い、技術系に進みました。技術系が最初に配属されるのは、研究所あるいは工場での勤務でしたが、私は商品開発研究所に配属され、炭酸飲料に関わりました。
2011年には技術研究所に異動し、飲料を工場で作る際のトラブルを解決するために、情報を解析。工場内にあるミニプラントでトラブルをシミュレーションし、解決につなげていました。
2017年からは生産部へ異動します。ここでは研究所の開発から、工場までの全工程をサポートし、品質・量産性を確保した設計となるよう、設計面に対してアドバイスをしています。製造時には、各部の情報を集約して工場に伝え、スムーズな立ち上げをサポートしてきました。
また、2016年頃から世界的に海洋プラスチックごみの話題が取り上げられるようになっていました。以前から、すでに社内で環境問題への取り組みはあったのですが、当社でもその流れに合わせて、環境への取り組みをより推進していくようになりました。
そのため自然と日常業務の中で、環境に関わる業務が増えていき、結果としてラベルレスの取り組みにも参加するにいたりました。そういった意味で、学生時代に研究していた汚染土壌改良の微生物の研究から今取り組んでいる環境負荷軽減の開発へ、環境を起点に過去と現在が結びついていると感じています。
昔から環境保全に取り組みたいと考えていたので、ラベルレスの取り組みに携われるという話を聞いてモチベーションが上がりました。環境のためだからこそ、最後まで実現に向けてやりきることができました。
ラベルレスボトルを目指し、現場と設計をつなぐ──お客様の笑顔のために
フルラベルレスボトルの計画は、生産部内では上司も含めて5名が参画しました。
最初は、タックシールをなくして、情報を載せる代替を何にするのか考えました。パターンを複数作成し、予算、期間を含めて話し合い、可能性を絞り込んでいきました。情報をキャップに載せるのか、ペットボトルに載せるのか、設計時から入れるのかなど、さまざまなアイデアが飛び交っていましたね。
当初は、資材メーカーでのキャップ製造時に情報を印刷してもらうことを考えました。しかし、コストが嵩むことや経済産業省の動向に鑑みて、別の方法に切り替えました。
次に成形後のボトルにレーザー印字することを検討しました。しかし設備仕様詳細の検討、製作期間、関連機器の準備に時間を要することが分かり、上市時期に間に合わない為に断念しました。最終的には納期やコストの観点も含め、ボトル成形すると同時に刻印を付与する形に落ち着きました。
製造では、試してみて気付くことの連続でしたね。それまでの経験やノウハウを活用するのは難しかったです。他社の既存技術をそのまま転用するのも難しいので、基本的には自分たちで進めなければなりません。多様なノウハウを持つ設備メーカーに協力してもらいながら、新しいことにチャレンジしていきました。
今回のフルラベルレスボトルで苦労したのは、マークの視認性をいかに高めるかです。
視認性が低いと、法令違反になってしまうので、その境を議論する時はドキドキしていましたね。やはり研究所と工場で作ったものには少し違いが出ます。工場での製造条件を考慮しつつ、最低限の視認性を確認します。もちろん自分としてはベストなものを出しているのですが、100点満点ではありませんでした。しかし、許容範囲という評価をいただけたので、ほっとしましたね。
達成感を得られるのは、販売後のお客様の反響です。
お客様により喜んでいただけるよう大事にしているのは、現場を見にいくことです。多くの場合、現場と設計のゴールは少しずれてしまうんです。設計は、お客様が最優先ですから、情報を見やすくしてほしいと要望を現場に伝えます。
しかし、工場側にとっては日常の稼働も大切です。そのため、生産性に目が行きやすくなり、つい効率を優先しがちです。そこをうまく調整していくのが、私の最大の役割です。会社としてもお客様が一番と考えていますから、そこはブレずにいきたいです。
製造の初めの立ち合いは、想定外の事象が発生することもありますから、ドキドキしかないです。なので、初めの立ち合いが終わるだけでもほっとした安心感があります。
上司からも「現場に行って、現物を見て、現実を確かめろ」とよく言われます。やはり、現場から得られるものは多いと思っています。
世界的な環境問題にも、消費者の日常生活にも、新しいラベルでアプローチ
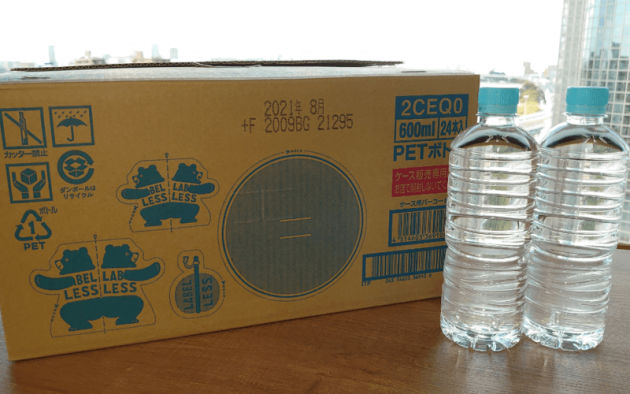
▲「アサヒ おいしい水」天然水 ラベルレスボトル。段ボールを切り取るとトントン相撲として遊べる
現状、感じている課題があります。
「ラベルレスボトル」商品は2020年現在、ケース販売専用商品として販売しています。今後は、より身近なスーパーなどで取り扱っていただけるよう、ラベルレスの更なる進化や、新たな価値を持つ容器包装を実現したいです。お客様の日常に寄り添い続けられるようにしていきたいですね。
実現に向けてのハードルは、新しいラベルの形を考えることです。単純にラベルの使用量を減らすと環境負荷軽減にはなりますが、ボトルへの接着性が下がり、現状当社で設けている品質基準を満たさなくなる可能性があります。一方で市場へ与えるインパクトは減ってしまうことも考えられます。各ポイントのバランスを踏まえながら、新しいラベルの形を考えています。
また、海洋プラスチックごみ問題が叫ばれている状況ですので、リサイクルでごみになる部分を減らすと同時に、将来的にはペット樹脂を使わないボトルを開発できたらいいなと個人的には考えています。アサヒ飲料では持続可能な容器包装の実現に向けた目標として「容器包装2030」を制定しています。その達成を目指し、生産部としてもペットボトル以外の方法を模索し続けます。
生産部には、工場を経験した人が多いですが、私は研究所経験者です。工場経験者は日常の生産活動の円滑化に強みがあります。しかし、私は研究所を経験しているからこそ、どうしたら新しいものをつくれるのかを常に考えています。その違いを生かして、モチベーションを高く持って挑戦したいです。
一方で、各部署でやらないといけないものや、目指すものは少しずつ違います。それを調整して製品に仕上げるのがわれわれの仕事です。それぞれが100%納得、とまではいかなくとも、各担当者が納得できた商品が世に出たときは、達成感と安堵感を覚えます。やりがいを感じる部分でもありますね。
何より嬉しいのは、「おいしかったよ」「なかなかない味だよね」「ラベルがないとラクでいいよね」など、実際に使っているお客様からの反響です。生活にダイレクトに届けられる点に、私の喜びがあります。
アサヒ飲料株式会社
この会社にアクションする